Typical working scenarios and applications of brushless motors.
The application fields of brushless motors are very wide, such as robots, smart homes, automobiles, power tools, industrial control, automation, modeling, and aerospace, etc. In general, applications in any field can be mainly divided into the following three scenarios:
·Continuous load application
·Variable load application
·Positioning application
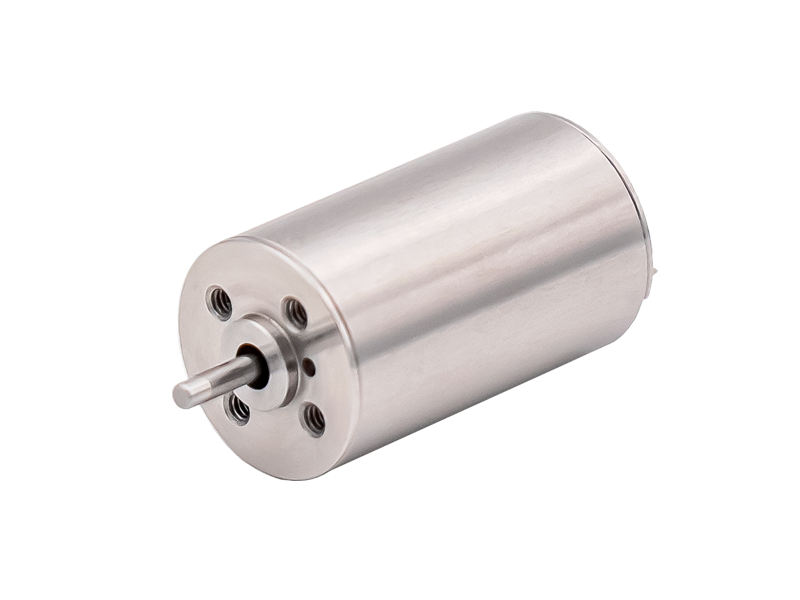
Continuous load application
This application is mainly used in fields that require a certain speed but do not require high speed accuracy, such as fans, water pumps, hair dryers, ordinary electric toys, massagers, adult products, and so on. Usually, these types of applications have relatively low costs and are mostly open-loop control.
Variable load application
This mainly refers to applications where the motor speed needs to vary within a certain range, and in such applications, there are higher requirements for the high-speed characteristics and dynamic response characteristics of the motor. Washing machines, dryers, and compressors in household appliances are good examples. In the automotive industry, oil pump control, electronic controllers, engine control, and electronic tools are also good examples. In the fields of high-end car models, competition level models, aircraft models, and drones, there are higher requirements for the speed and performance of motors. There are also many applications in the aviation field, such as centrifuges, pumps, robotic arms, gyroscopes, and so on. In this field, motor feedback devices are commonly used to form semi open and closed loops for control. This requires complex control algorithms, which increase the complexity of the controller and also increase the system cost.
Positioning application
Most applications in industrial control and automatic control belong to this category. In these applications, energy transmission is often completed, such as gears or conveyor belts, so the system has special requirements for the dynamic response and torque of the motor speed. At the same time, these applications may also need to change the direction of the motor at any time. The motor may work in constant speed, acceleration, and reduction stages, and the load may also change during these stages. Therefore, higher requirements are put forward for the controller. Usually, this type of control uses closed-loop control, and there may even be three control loops: torque loop, speed loop, and position loop. During speed measurement, photoelectric encoders and some synchronization devices may be used. Sometimes these sensors are used to measure relative position, and sometimes they are used to measure absolute position. Process control, mechanical control, and transportation control all belong to this category of applications.