The difference between inductive and non inductive brushless DC motors.
1. What is feeling?
What is "Hall sensor" in the context of tactile brushless technology? Hall refers to the Hall effect, a phenomenon discovered by American physicist A.H. Hall (1855-1938) in 1879 while studying the conductive mechanisms of metals. When current passes through a conductor perpendicular to the external magnetic field, a potential difference occurs between the two end faces of the conductor perpendicular to the direction of the magnetic field and current, which is known as the Hall effect. This potential difference is also known as the Hall potential difference. Simply put, through Hall sensors, the brushless driver can clearly determine the position of the rotor of the brushless motor.
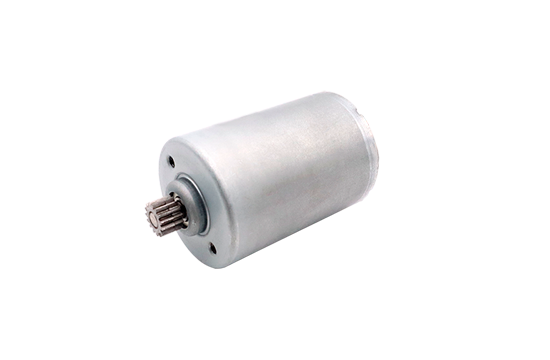
2. What is insensitivity?
Non inductive brushless refers to the absence of Hall sensors. In the absence of direct feedback, a non inductive brushless motor can only indirectly obtain the rotor position of the motor. Common methods include back electromotive force method, inductance method, magnetic flux method, high-frequency pulse method, and other intelligent methods. The most commonly used method is back electromotive force method.
When starting a sensorless brushless motor, the orientation of the rotor magnetic poles is unknown, so the current can only be randomly changed to drive the motor. Similar to "Meng", there is always a time when the rotor will roll, and after the rotor rolls, the position of the rotor can be calculated based on the change in current on the coil, and then the current and direction can be controlled. That's why there are always clicking symptoms when starting without feeling or brushing.
However, the difference lies in the presence of sensors and brushless drives. With sensors, the driver knows the orientation of the rotor magnetic poles from the moment it is turned on, and can directly supply the corresponding current to the corresponding coil to drive the rotor. But when the current is very low, the motor will make a continuous creaking sound. That's why induction motors will hear a continuous creaking sound at low speeds, while non induction motors won't.
Advantages and disadvantages of brushless technology
The advantages of brushless motors include better linearity, strong speed stability, and high responsiveness.
Defects of brushless technology: high cost and difficulty in waterproofing. Due to the limitations of Hall sensors, they are prone to interference, which can cause the driver to receive incorrect information and lead to malfunctions. Therefore, the wire length from the driver to the motor is generally limited to within 5 meters.
Advantages and disadvantages of seamless and brushless technology
Advantages: No sensors, lower cost, and line length not limited by Hall factors.
Defects: Linearity is not as good as inductive brushless motors, and in addition, drivers on the market may have errors of ± 20 revolutions per minute or more due to inaccurate speed feedback. It is easy to shake or fail to start when loaded or fully loaded.
The Topband brushless motor system, using FOC control, has the following advantages:
Fast self-learning in 100 seconds, suitable for various three-phase motors, with little need for manual adjustment; Dual virtual encoder technology, even without excitation, the motor state can still be known, perfectly solving the problems of startup jitter and failure under load and full load.
Space vector modulation technology, speed and current dual closed loops, self-developed ultra fast initial position identification algorithm, and strong anti-interference speed loop control algorithm make it have the characteristics of smooth start-up, high speed ratio, low speed fluctuation, and high efficiency and energy saving. The speed fluctuation is within ± 0.5~± 1 RPM.
Input voltage AC220V, power range: 50~5000W, speed range: 30RPM~rated speed, up to 30000RPM, supports user customization
Complete fault diagnosis and protection measures, with torque limiting function
More than 20 monitored items such as current speed and current
Supports RS232/RS485 communication with standard ModBus RTU protocol, enabling multiple drivers to run online (up to 255), and can customize CAN bus.