Analysis of Control Methods for Brushless DC Motors.
Brushless DC motor is developed on the basis of brushed DC motor, which has the advantages of stepless speed regulation, wide speed regulation range, strong overload capacity, good linearity, long service life, small size, light weight, and large output. It solves a series of problems existing in brushed motors and is widely used in various fields such as industrial equipment, instruments and meters, household appliances, robots, medical equipment, etc. Due to the absence of brushes for automatic commutation in brushless motors, electronic commutators are required for commutation. The brushless DC motor driver achieves the function of electronic commutation.
There are currently three mainstream control methods for brushless motors:
1. Square wave control:
Also known as trapezoidal wave control, 120 ° control, 6-step directional control
The advantages of square wave control method are simple control algorithm, low hardware cost, and the ability to achieve high motor speed using a controller with ordinary performance; The disadvantages are large torque fluctuations, presence of certain current noise, and inability to achieve maximum efficiency. Square wave control is suitable for situations where the requirements for motor rotation performance are not high. Square wave control uses Hall sensors or sensorless estimation algorithms to obtain the position of the motor rotor, and then performs 6 reversals (every 60 °) within a 360 ° electrical cycle based on the rotor position. Each reversing position motor outputs a specific direction of force, so it can be said that the position accuracy of square wave control is 60 ° electrical. Due to the fact that the phase current waveform of the motor is close to a square wave under this control method, it is called square wave control.
2. Sine wave control:
The sine wave control method uses SVPWM waves, which output a 3-phase sine wave voltage, and the corresponding current is also a sine wave current. This method does not have the concept of square wave controlled commutation, or assumes that an infinite number of reversals are performed within one electrical cycle. Obviously, compared to square wave control, sine wave control has smaller torque fluctuations and fewer current harmonics, making it feel more "delicate" to control. However, the performance requirements for the controller are slightly higher than square wave control, and the motor efficiency cannot be maximized.
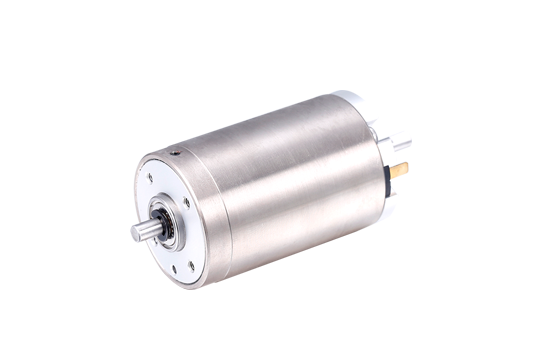
3. FOC control
Also known as vector frequency conversion, magnetic field vector directional control, and C control
Sine wave control achieves voltage vector control and indirectly controls the magnitude of current, but cannot control the direction of current. The FOC control method can be considered as an upgraded version of sine wave control, which realizes the control of current vector, that is, the vector control of motor stator magnetic field.
Due to the control of the direction of the motor stator magnetic field, the stator magnetic field and rotor magnetic field of the motor can be kept at 90 ° at all times, achieving maximum torque output under a certain current. The advantages of FOC control method are: small torque fluctuation, high efficiency, low noise, and fast dynamic response; The disadvantages are: high hardware cost, high requirements for controller performance, and need to match motor parameters.
So, which approach is more suitable for future development? FOC is currently the best choice for efficient control of brushless DC motors (BLDC) and permanent magnet synchronous motors (PMSM). FOC precisely controls the magnitude and direction of the magnetic field, resulting in smooth motor torque, low noise, high efficiency, and high-speed dynamic response.
Due to the obvious advantages of FOC, many companies have gradually replaced traditional product control methods with FOC in various applications.